Dit zijn de 10 meest kortgesloten aandelen op de ASX
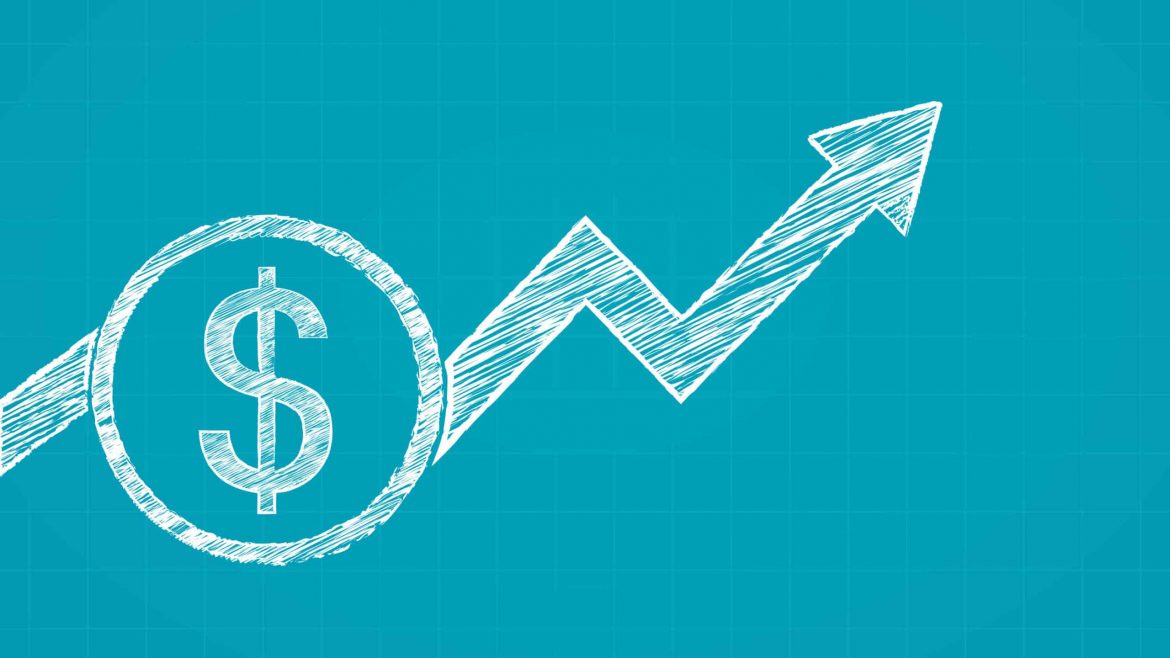
Kogan.com Ltd (ASX: KGN) en Zip Co Ltd (ASX: Z1P) aandelen behoren deze week tot de meest short-short aandelen op de ASX …
Aan het begin van elke week kijk ik graag naar het shortpositierapport van ASIC om erachter te komen welke aandelen het doelwit zijn van short sellers.
Dit komt omdat ik denk dat het de moeite waard is om de korte rente goed in de gaten te houden, aangezien hoge niveaus soms een teken kunnen zijn dat er iets niet klopt met een bedrijf.
Met dat in gedachten, zijn hier de 10 meest short-aandelen op de ASX deze week volgens ASIC:
Kogan.com Ltd (ASX: KGN) is het aandeel met de hoogste shortpositie op de Australische aandelenmarkt geworden nadat het korte belang toenam tot 11,6%. De aandelen van dit e-commercebedrijf zijn sterk onder druk komen te staan als gevolg van voorraadproblemen en een vertraging van de verkoop. Short sellers lijken niet te geloven dat het ergste voorbij is.
Flight Center Travel Group Ltd (ASX: FLT) heeft zijn korte rente licht zien stijgen tot 10,4%. Bezorgdheid over een haperend herstel op de reismarkt woog op het beleggerssentiment. Vooral gezien de huidige Victoriaanse lockdown.
Resolute Mining Limited (ASX: RSG) zag de korte rente week op week weer stijgen tot 10,3%. Regelgevingskwesties bij de Bibiani-vestiging in Ghana, teleurstellende productieprestaties en ondermaatse begeleiding hebben allemaal invloed op de aandelen. KPN aandelen kopen kan online.
Webjet Limited (ASX: WEB) heeft zijn korte rente zien stijgen tot 10,2%. De Victoriaanse lockdown, bezorgdheid over de waardering en de vrees voor verlaging van de commissie voor reisbureaus kunnen de oorzaak zijn van deze recente stijging.
Tassal Group Limited (ASX: TGR) heeft een korte rente van 9,6%, wat week op week weer vlak is. De aandelen van Tassal zijn grotendeels onder druk komen te staan door de zwakke zalmprijzen.
Bij Temple & Webster Group Ltd (ASX: TPW) is de korte rente afgenomen tot 9,4%. Deze online meubel- en huishoudartikelenretailer was het doelwit van short sellers vanwege zijn plannen om zwaar te investeren in zijn toekomstige groei ten koste van de marges.
Electro Optic Systems Hldg Ltd (ASX: EOS) heeft 8,3% van haar aandelen short. Dit is van week tot week plat. Dit kan mogelijk te wijten zijn aan bezorgdheid dat de prestaties van het communicatie-, defensie- en ruimtevaartbedrijf zullen worden beïnvloed door problemen met de toeleveringsketen.
Megaport Ltd (ASX: MP1) heeft een korte rente van 8,3%, die week op week weer stijgt. Hoewel de Network as a Service-provider sterk blijft groeien, lijken sommige short sellers te denken dat zijn aandelen overgewaardeerd zijn.
Inghams Group Ltd (ASX: ING) heeft 8% van haar aandelen short, wat week op week vlak is. Helaas voor short sellers gaf de pluimveeproducent vorige week winstverwachtingen die ruim boven de marktverwachtingen lagen.
Zip Co Ltd (ASX: Z1P) is terug in de top tien met een korte rente van 7,8%. Vorige week behielden analisten bij UBS hun verkooprating en verlaagden hun koersdoel tot $ 5,60. De makelaar maakte de stap vanwege zorgen over de margedruk als gevolg van toenemende concurrentie.
Vraagt u zich af waar u nu $ 1.000 moet investeren?
Als beleggingsexpert Scott Phillips een aandelentip heeft, kan het lonend zijn om te luisteren. De vlaggenschip Motley Fool Share Advisor-nieuwsbrief die hij al meer dan acht jaar beheert, heeft tenslotte duizenden betalende leden voorzien van een verdubbelde, verdrievoudigde of zelfs meer aandelenselectie. Aandelen koers Galapagos is gestegen.
Scott heeft zojuist onthuld wat volgens hem de vijf beste ASX-aandelen kunnen zijn die beleggers nu kunnen kopen. Deze aandelen worden verhandeld tegen bijna spotgoedkope prijzen en Scott denkt dat ze op dit moment geweldige aankopen kunnen zijn.